The crown/profile of the strip rolled at No.1 HSM was different from that of No.2 HSM was the first impression to me. I felt the crown of No.1HSM’s strip was flatter at the body/center portion and steeper thinning at the edge portion compared to that of No.2 HSM’s strip.
After I became an engineer of technical group at No.1 HSM, there emerged a severe demand from a big customer which was a specialty steel producer of high carbon low alloyed steel for round blade saw through cold rolling and heat treatment. Their demand was to reduce the strip crown from 120μ to 60μ and under between center and 25mm from edge. They slit hot coils from our mill to two narrow coils which were cold rolled. When strip crown was big, the cold rolled strip cambered too much. Originally allowance of thickness of specialty steel was smaller than that of ordinary carbon steel and they trimmed big amount of edge portion to assure thickness and prevent camber.
But there was no effective way to guarantee small crown value such as under 60μ in the days without crown control device such as roll bender, CVC shifting or Pair-cross mill.
I was very confused how to cope with customer’s extreme demand.
One day, when I was wondering how to reduce strip crown, a new idea sprang to my mind. Strip crown of No.1 HSM was flat or small thickness difference at body portion and drastic thinning or big thickness difference at edge portion.
So, extreme small work roll diameter at edge portion could reduce the drastic thinning of rolled strip. Based on this idea I calculated the flattening amount of work roll and decided EL and EH considering the strip profiles.
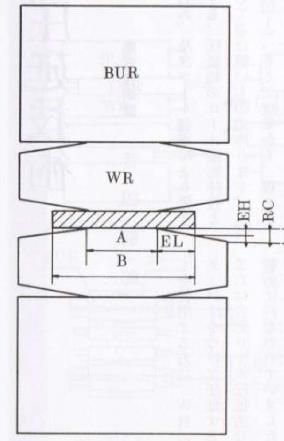
I explained my idea and asked to the hot strip mill manager to do an experiment to evaluate it. I anticipated his denial, because the difference between conventional small sine curve and taper crown curve is extraordinary big and it would cause cobble at finisher stands or coiler. In 1970s even a small change of roll crown was a big issue for hot strip mills.
But surprisingly he accepted my idea. It was very lucky for me.
The 1st experiment;
I was very prudent to go ahead with taper roll idea. The difference between ordinary sine roll curve with small amount and taper roll curve was very big and so there might have happened big flatness trouble which resulted in cobble in finisher stands caused by a young engineer’ idea.
So I started the trial at only last stand with small EH of 30μ to prevent cobble and EL of 200mm. EL was decided based on the typical profile of the mill by my instinct. Four slabs with the same specification and same size were scheduled at the top of a finisher rolling campaign and at first two slabs were rolled with the taper work roll and after F6 work roll change the remaining two slabs were rolled with an ordinary sine curve and rolling continued till the end of the campaign. There occurred no trouble and no flatness problem. Samples to measure the crown value were taken from the coils at the point of 10m from the tail end. We had not a profile meter in those days and samples were measured by micrometer manually.
Strip crown were reduced in low carbon steel with 3.8mm*929mm by 12μ, 107μ and 110μ by taper roll and 124μ and 118μ by ordinary sine curve roll respectively.
The 2nd experiment;
Strip crown was reduced and flatness was not deteriorated at the first experiment and so I ventured to increase EH to 60μ. This time strip crown was reduced by 34μ and we experienced very big center buckle on the run out table, but after skin-pass rolling deteriorated flatness was corrected.
The 3rd experiment;
In the 1st and 2nd experiments I used coils for cold rolling mill. Two experiments revealed good results and so I used 4 slabs in the 3rd experiment. One coil was for pickled and oiled coil. There were no troubles.
The 4th experiment;
The three experiments seemed successful. Strip crown were greatly reduced and flatness problem did not happen.
So, I decided to use taper roll through one rolling campaign to study the change of strip crown, edge drop, strip flatness, work roll wear and so on.
On the day of the 4th experiment (taper roll at F6 and the same EL and EH as 2nd and 3rd experiments) I stationed myself at finisher pulpit to provide direction to the finisher mill operators and to watch strip flatness and instability. At the pulpit I watched the rolled strips with heavy center buckle after F6. Small reduction changes at latter stands could not reduce the heavy center buckles. My heart beat fast to image lots of damaged shape coils in the processing lines. In the 2nd and 3rd experiments my heart did not beat fast, because center buckled coils were only two to four coils. I only watched lots of coils were rolled with deteriorated shape before me. Then the assistant manager of No.1 HSM ran up to the pulpit and told me to stop the experiment. I told him, we had already rolled more than half of the campaign so it was no use to stop the experiment. I continued the experiment.
I worried about what I did. At that time we had May holidays in Japan, but I was at skin-pass mill to watch all coils of the experiment. Before skin pass all coils had heavy center buckle or C camber, but skin pass mill corrected the deteriorated shape. Lots of coils happened to be the coils for export. I watched the coils were corrected before my eyes, but I feared the existence of internal stress and occurrence of troubles at customer’s plant for three months. Finally there were no claims at all. I was liberated from the fear.
The 5th to 8th experiments,
To solve the problem of the center buckle I increased the stands with taper rolls.
Experiments with taper rolls at F5 and F6 were done, but medium size center buckle still existed.
Experiments with taper rolls at F4, F5 and conventional small sine curve roll at F6 were done, and center buckle disappeared.
Both sides taper roll rolling was adopted for the production of high carbon low alloyed steel and stainless steel to satisfy the customer’s demand for 6 years until the installation of work roll shifting that used one side taper roll to cope with the width change in one rolling campaign and also cyclic shifting for tin plate hot coil to prevent high-spot problem that caused sticking at tin mill.